Examining the Evidence
When a customer approached Pennsy Corporation about a problem they were having with premature wheel and brake wear on certain double stack intermodal cars, Pennsy engineers jumped right in and got their hands dirty. Via photographs and on-site inspections, the customer shared examples of the worn parts and the cars from which they came.
Diagnosing the Problem… and the Costs
A quick and thorough investigation of the parts and the problematic cars revealed that increased friction in the handbrake rigging was preventing the brakes from fully releasing on the inboard trucks. Measurement and testing showed that these suspect cars were exhibiting a release of braking pressure in the order of only 13%, whereas a 100% release was desirable.
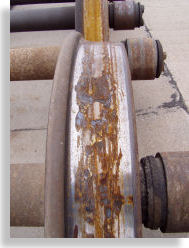
This made for a costly situation for the customer. Besides the immediately obvious high costs related to the frequent replacement of worn wheels and brakes, there were the additional factors of the increased down time for service that affected the overall profitability of the cars. The carriers were also impacted due to increased fuel consumption consistent with the greater drag these underperforming cars placed on the run. To paint an even bleaker picture, it appeared that the problems grew worse as the cars aged.
An Innovative Approach to Reducing Friction
It became clear that a much higher degree of brake pressure release was needed and identifying and reducing friction in key areas of the brake rigging was the means by which to achieve this goal. Working directly with the customer, Pennsy engineers established a straightforward set of criteria for achieving this, namely to develop a solution to the handbrake rigging friction problems that was low cost and that could be easily implemented so as to minimize the overall downtime for the railcars.
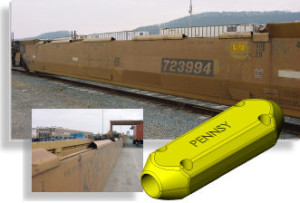
Better Than New?
Almost immediately, Pennsy engineers saw that they were on the right track. Testing of initial concepts and designs showed marked improvements in friction reduction and resulting brake release. With ongoing collaboration between Pennsy and the customer, revisions were made to optimize the final shape and application method until the final component design was ready.
Comprehensive testing of the finished part yielded a measurable release of 98% of braking pressure in an 11-year-old rail car, compared to a 97% measured release in a brand new car with the same type of brake rigging assembly.
Pennsy’s efforts and creativity yielded a highly practical and effective solution that, in the grander view of the project, significantly reduced down time and maintenance costs, translating into increased profitability for the customer.
Getting Pennsy Involved on Your Project
For over two decades Pennsy Corporation has designed and marketed innovative products to meet the specialized needs of the railroad industry. Our team of engineers has a combined service of over 120 years in the locomotive, freight and transit segments of the railroad industry. Pennsy excels in solving engineering problems using innovative thinking together with the latest technologies and in-house testing facilities for validation of new products. Our four-step R&D, Design, Testing and Manufacturing process enables us to collaborate closely and effectively with engineering divisions of major railroads, freight car builders and shippers to deliver the right solution.
This process ensures our customers the lowest total cost design solutions by providing quality products and reducing the overall application and maintenance cost of customer equipment.
To get the Pennsy team involved in addressing your railroad specific needs, contact Pennsy at questions@pennsy.com.